CAE回彈補償技術在CS95高強度鋼梁類模具開發中的應用
陳俊,曾兵華,江明潔
摘要:本文結合高強度鋼艙邊梁后段的成形工藝難點和回彈較大的特點,利用CAE分析技術對其進行全工序分析和回彈分析,對其成形缺陷和回彈趨勢進行了有效的預測。同時對回彈產生的原因進行分析,制定合理的回彈補償方案,并運用CAE反向回彈補償技術對模具型面進行補償,補償后CAE驗證回彈均在要求的+-0.5mm之內;將回彈補償后的模具型面進行加工,經該模具生產的樣件的尺寸精度滿足要求且樣件的合格率達92.46%,為高強度鋼梁類零件的CAE回彈補償提供了一定的參考。
關鍵詞:高強度鋼;艙邊梁后段;回彈分析;回彈補償
The application of CAE springback compensation technology on CS95 high strength steel beam mold development
Abstract: In this paper, the forming process and springback analysis of the side beam rear section on the high strength steel are studied by means of CAE analysis technology. The forming defects and springback trend are predicted effectively, and the reasonable springback compensation scheme is formulated based on springback. The die surface is compensated by using CAE inverse springback compensation technology. The value of springback is within the requirements. The precision of sample produced by mold after the compensation of springback meets the requirement and the qualification rate of sample is 92.46%. It provides a certain reference for CAE springback compensation of high strength steel beam parts.
Key words: high strength steel; rear section of the side beam; springback analysis; springback compensation
隨著人類經濟水平的提高,人類所面臨的環境和能源危機問題也日益加重,再加上人類對優質產品的追求,使制造業的發展突飛猛進,汽車行業也如此[1]。近年來汽車行業的發展非常迅速,為了解決以上難題,各種各樣的新型制造技術、新工藝層出不窮,其中最有效的新技術是以先進的高強度鋼板和先進的制造技術相結合的汽車輕量化技術。
汽車輕量化技術不僅僅是單純的從減輕汽車的重量方面來考慮,它是在保證各種汽車安全性能的前提下通過應用輕質材料或特殊材料與優化汽車車體結構相結合來降低汽車自重的一種方法[2]。當前汽車輕量化技術主要通過汽車結構優化、輕質材料的應用和采用高強度鋼板的制造技術來實現。在以上的幾種實現途徑中,重新設計車體結構花費的成本較高且車體結構的優化空間較小;輕質材料的應用比例越來越高,但由于材料自身存在缺陷很難在短期內得到大規模的應用;與這兩種技術相比,高強度鋼板的制造技術的應用前景更為廣闊[3]。
高強度鋼板在汽車輕量化技術中的應用主要是通過采用較薄的高強度鋼板來替代較厚的低碳鋼板,從而達到減輕重量的目的[4]。在力學性能方面,高強度鋼和普通低碳鋼存在較大的差異,因其較高的強度和較低的塑性使其在相同的工藝條件下比普通的鋼板更易破裂且回彈較大,難以保證產品的尺寸和形狀精度[5]。其回彈產生的原因主要有以下幾個:
(1)板料的成形不夠,成形結束時制件的某些區域還處于彈性變形階段,彈性變形恢復導致產生回彈。
(2)板料在成形過程中,產生塑性變形的同時伴隨著彈性變形的產生,在板料成形結束后隨著彈性變形的消失同樣會產生回彈。
(3)板料在成形結束時內表面處于受壓的應力狀態,外表面處于受拉的應力狀態,當外力卸載后由于制件內、外表面存在的壓差而產生回彈。
近年來板料成形CAE分析技術飛速發展,不僅有助于高強度鋼板的設計優化和模具的開發,還能準確有效的進行板料的成形性分析和回彈分析預測。采用可靠的材料參數來進行合理的CAE分析,預測的回彈趨勢和實際的檢測結果基本一致。因此根據CAE分析結果,在前期的設計階段制定合理的回彈補償方案和在后期開展回彈補償,能更好地開發高強度鋼模具,同時也能縮短模具的開發周期和減少模具的整改次數。
本文以艙邊梁后段零件為例,從產品的沖壓工藝設計方面入手,結合CAE分析及回彈補償技術,在設計階段完成型面的回彈補償工作。并結合實際生產進行效果驗證,積累了高強度鋼板梁類零件回彈問題解決方法的寶貴經驗,為解決此類問題提供了很好的參考作用。
2、零件的工藝性及有限元分析
圖1為長安CS95車型的艙邊梁后段零件,所用材料為B340-590DP,具體材料參數如表1所示,零件的厚度為2.2mm;該零件為重要的汽車車體結構件,主要作用是承載、防止車體變形和吸收沖擊能量等。由圖可以看出,該零件呈“S”型,底面為曲面,很容易產生扭曲變形;兩側壁的間距是中間大兩端小,且拉延深度為145mm,通常情況下成形較為困難,中間位置很容易開裂、兩端位置很容易起皺,采用常規的成形方式難以控制零件側壁的質量和零件的扭曲變形,故采用拉延成形方式;此外由表1可知,材料的屈服強度和抗拉強度較大,故通常情況下零件的回彈也較大。為了控制零件的回彈和扭曲變形,必須在設計工藝型面時考慮利用CAE軟件對零件進行回彈補償,且往往需要迭代多次才能達到較為理想的結果,加上零件較厚,需要在后工序增加整形工序來校正零件。因此根據零件自身的結構特點和工藝性,再結合實際的生產情況,可將零件的沖壓工藝過程進行如下排布:工序一,拉延;工序二,切邊+沖孔;工序三,側整形;工序四,切邊+沖孔+側切邊+側沖孔。
圖1 艙邊梁后段零件
表1 B340-590DP鋼的材料參數
屈服強度/MPa
|
抗拉強度/MPa
|
n值
|
r值
|
0°
|
45°
|
90°
|
|
646
|
0.188
|
0.93
|
0.9
|
1
|
2.2 全工序成形和回彈分析
CAE回彈補償技術的前提是要先對零件的回彈趨勢和回彈量進行預測,即利用CAE模擬軟件對零件進行全工序成形及回彈分析,確保零件成形狀態良好,在工藝設計階段對可能出現的缺陷進行預測并消除,為回彈補償提供較為可靠的依據[7]。
該零件采用AutoForm軟件來進行CAE數模模擬分析,拉延工序的有限元分析模型如圖2所示,板料料厚為2.2mm,摩擦系數為0.15,壓邊力為120T;為了使拉延之后的零件能夠更好地貼合后工序模具,拉延要考慮縮放比例;考慮要進行回彈分析和后續的回彈補償,所以采用AutoForm軟件最精密的模擬參數設置模式-FV最終驗證模式,同時網格模型為EPS-11彈塑性殼單元。
圖2 拉延工序的有限元分析模型
零件的重力加載情況如圖3所示,在零件的重力加載階段,板料只受到重力的影響,該階段要求板料無明顯的上凸和下塌等附加變形,避免板料在壓邊圈閉合過程中由于材料的流動不均勻而造成零件的起皺或開裂,由圖3可知板料在此過程中較為平整,無附加變形。
圖3 零件的重力加載情況
在板料的沖壓成形過程中,需要利用壓邊圈來控制板料的流動,從而使板料能夠均勻地流動來防止板料的起皺,所以壓邊圈的閉合過程不能有起皺翹曲等現象,壓邊圈的壓邊力為120T,壓邊圈閉合過程中板料的變形情況如圖4所示,由圖知板料在此過程中無起皺翹曲現象產生。
圖4 壓邊圈閉合時板料的變形情況
經多次反復模擬分析得到了拉延工序零件如圖5所示,由圖可以看出,零件的成形較為充分,無起皺和開裂現象且成形過程板料流動情況較為均勻。
圖5 拉延成形后的零件
經過后續的切邊沖孔和整形工序之后,得到最終的零件如圖6所示,由圖可知,切邊沖孔和整形工序后的零件不皺不裂,這是進行零件回彈分析的基礎。
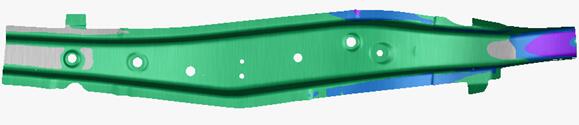
圖6 最終的零件
零件的全工序分析通過后,對零件進行回彈分析。首先對零件進行自由回彈分析來判斷零件的回彈趨勢,零件從第一工序到第四工序的回彈結果如圖7所示。由圖可知,零件各工序的回彈趨勢比較一致;在OP10拉延成形后,零件有幾個局部區域的回彈較大,主要集中在零件的兩端和側壁位置;經過OP20切邊之后由于應力釋放使側壁的回彈值有所上升,其它位置的回彈變化不大;零件在OP30整形后側壁的回彈值有減少趨勢,但兩端的回彈值增加,特別是零件前端的法蘭部分;零件在OP40進行局部的切邊和沖孔,該工序屬于零件的應力釋放過程,回彈值變化不大。
圖7 零件各工序的回彈
回彈補償原理[8]:利用有限元數值模擬計算回彈,然后在預估有回彈的區域作出反方向的補償值,使零件成形后的反彈正好與補償值抵消,從而得到合格產品。
由以上零件的全工序成形分析結果可知,零件成形狀態比較穩定,沒有起皺和開裂現象;由零件的回彈分析結果可知,零件的回彈主要產生于前三工序,故初步設定三種補償方案。
方案一:只補償拉延工序;
方案二:只補償第三工序,即整形工序;
方案三:補償前三工序。
下面將根據這三種補償方案來進行回彈補償,最后選擇一種較為合理的補償方案,回彈補償選擇最終驗證-FV模式進行計算,選擇EPS彈塑性殼單元,最大單元角度為22.5°,最大料片網格細化等級為6,采用運動硬化模型的材料和求解器,模具網格保證在90°R角至少有8個單元。
方案一:只補償拉延工序,補償區域如圖8所示,型面劃分為補償區域、過渡區域和固定區域。先嘗試用1作為補償系數,對比補償迭代兩次的結果如圖9所示,由回彈結果對比可知,迭代第一次、迭代第二次的回彈結果相比產品原來的回彈均有所改善,在零件前端區域和法蘭區域的回彈值還是比較大,且第二次迭代結果整體上比第一次的結果稍差,補償效果不太理想。
圖8 方案一補償區域
圖9 方案一補償系數為1的回彈補償結果
再次嘗試進行補償系數為0.8的補償,其補償后的回彈結果如圖10所示,由回彈補償的結果可知,兩次迭代的補償效果均比補償系數為1的效果好,但是零件的法蘭區域的回彈還是較大,還需要改善。再嘗試用補償系數為0.9、1.1和1.2來進行補償,補償效果均不如補償系數為0.8的,所以最終確定選用0.8作為最佳的補償系數來進行其它方案的補償。
圖10 方案一補償系數為0.8的回彈補償結果
3.2補償第三工序
方案二:補償第三工序(整形工序),補償系數為0.8,補償區域如圖11所示,補償后的回彈結果如圖12所示,由回彈補償的結果知僅對整形工序進行補償,效果和只補償拉延差不多,法蘭區域的回彈值減小但側壁的回彈值增大,法蘭區域的回彈如圖13所示,所以該補償方案效果也不明顯。
圖11 方案二補償區域
圖12 方案二補償系數為0.8的回彈補償結果
圖13 方案二補償系數為0.8的側壁回彈結果
方案三:補償前三工序,補償系數為0.8,補償后的回彈結果如圖14所示,由回彈補償的結果知,將補償迭代一次后,零件的回彈只有前端小片區域和法蘭部分較大,其它區域的回彈均較小;將補償迭代第二次后,除了零件前端小片區域外其它各區域的回彈均在+-0.5mm之內,達到了回彈補償的理想要求,最終采用該方案迭代兩次的數據。
為了保證型面質量達到加工要求,需對回彈補償的型面進行A面重構后再次驗證,驗證結果和方案三迭代第二次的回彈結果一致,證明了回彈補償結果的準確性。
圖14 方案三補償系數為0.8的回彈補償結果
3.4模具的加工、制造及補償效果驗證
采用回彈補償后的模具型面進行加工、制造,得到如圖15所示的高強度鋼艙邊梁后段模具。
圖15 高強度鋼艙邊梁后段模具
將模具進行裝配、調試后,生產的零件在檢具上檢測狀態如圖16所示,由圖知該樣件無起皺和開裂現象,幾個關鍵部位的尺寸精度檢測均合格,合格率達92.64%,滿足裝車要求。
圖16 成形樣件關鍵部位的檢測
4結論
(1)利用CAE分析技術可進行零件的全工序分析和回彈分析,能夠準確、有效地對零件的成形缺陷和回彈趨勢進行預測,為后續的模具型面回彈補償提供理論基礎;
(2)根據零件的特點和前期CAE分析得出的回彈結果,制定合理的回彈補償方案,并運用CAE反向回彈補償技術對模具型面進行補償,補償后CAE驗證回彈均在要求的+-0.5mm之內,有效的解決高強度鋼板回彈大的問題;
(3)對樣件進行檢測,尺寸精度在合格范圍內,樣件的合格率達92.64%,驗證了CAE回彈補償技術的準確性,為CAE回彈補償技術在高強度鋼梁類零件上的應用提供一定的參考。
參考文獻:
[1]李彥波,劉紅武 汽車輕量化沖壓技術及其數值模擬[J]計算機輔助工程,2013(6):90-94.
[2]岳博,徐晶才 汽車輕量化技術的進步與展望 [J]世界制造技術與裝備市場,:2015(5):100-102.
[3]楊亙,夏琴香,邱遵文,葉福源 高強鋼板在汽車上的應用及沖壓成形性能研究現狀[J]現代制造工程,2017(7) :138-143.
[4]Yan Zhang,et al. Lightweight Design of AutomobileComponent Using High Strength Steel Based on DentResistance[J].Materials and Design,2006,27:64-68.
[5]方剛 高強度鋼板沖壓成形性能及回彈特性的研究 [M]重慶:重慶大學,2011.
[6]李悅 汽車用高強度鋼的發展[J]汽車工藝與材料,2012(9):36-42.
[7]常桂靜,曾兵華,江明潔,陳身武 縱梁前段全工序回彈預測與控制[J]精密成形工程,2015(4):37-41.
[8]宋灝,畢大森,李超,關嘯基于位移回彈補償原理的汽車加強板回彈補償研究[J]重 型 機 械,2015(1):49-52.
|